In efforts to ramp up efficiency, reduce waste, and address skilled labor shortages, industrialized construction may be the answer. This approach shifts on-site work away from the jobsite where building components are produced in a factory off-site and shipped to the jobsite.
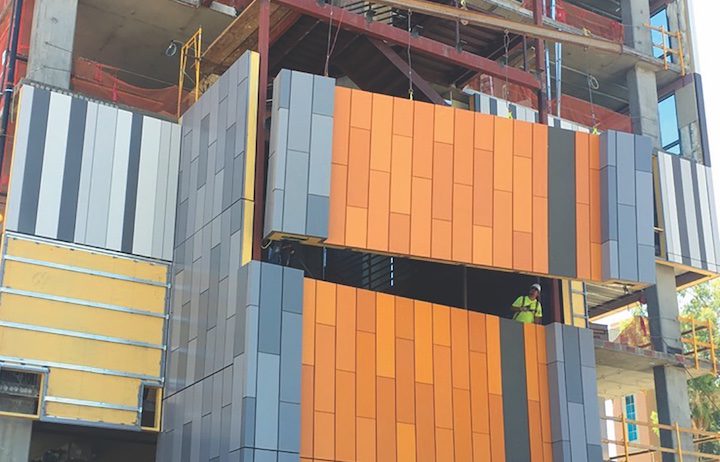
Hilton Canopy Hotel in Tempe, Arizona, utilizes two tested and proven systems: StoPanel Classic NExT ci and StoPanel Dri-Design. Dri-Design metal panels were installed in a specific pattern that represented the notes of the Arizona State University fight song.
Producing construction products, like wall panels or 3D-printed building components, in a controlled environment allows for a standardization that is executed with efficiency when done repetitively as production time and waste is reduced while workflows are optimized. The principles of industrialization, much like in the manufacturing industry, are essentially applied to the construction industry.
Commercial, industrial and even residential applications can stand to benefit. Per Construction Business Owner,
New opportunities in the commercial sector are being explored. Asset classes, such as office and retail, are being added to the usual candidates of multifamily—hotels, mixed-use structures and hospitals—all of which have building components that can be standardized for replicated application. This doesn’t mean that all of the buildings have to look the same. The structural and foundational components of walls, floors, ceilings and roofs of the buildings can be constructed using industrialized methods while still allowing for customized finishes.
An approach to industrialized constructions can also include design for manufacturing and assembly (DfMA). Per Designing Buildings,
By simplifying the design of a product, it is possible to manufacture and assemble it more efficiently, in the minimum time and at a lower cost. Traditionally, DfMA has been applied to sectors such as the design of automotive and consumer products, both of which need to efficiently produce high quality products in large numbers. More recently, construction contractors have begun to adopt DfMA for the off-site prefabrication of construction components such as concrete floor slabs, structural columns and beams, and so on.
Data and technology can play a huge role, which is where the borrowing ideas from the manufacturing industry come to a halt. This means a different approach to traditional thinking, shifting to a digital mindset. Per Autodesk,
Data is key to this kind of transformation. Each member of the team, from designer through builder to owner, needs to be able to see and use a common data set for the project. That makes BIM essential. “Nowadays with BIM we’re able to have a much more controlled grasp of what’s going into our buildings and get the level of detail that you need to deliver a building as a manufactured product,” [Brandon] Ionata [of StrucSoft Solutions] says.
With some sectors facing tighter timelines, and the ever-present need for more affordable housing, building in a sustainable manner that can keep up with demand can benefit from industrialized construction. With enhanced safety and less on-site activity required, the current need for social distancing is also more easily met.